Predictive Maintenance: How Smart Enterprises Cut Downtime and Maximize ROI
- John Jordan
- Apr 2
- 7 min read
The Rising Cost of Downtime—and the Predictive Solution
Unplanned downtime remains one of the most pressing challenges for modern enterprises, cutting across industries such as manufacturing, energy, logistics, and utilities. These interruptions do more than halt production; they damage reputations, create cascading delays, and inflate operational costs. According to industry benchmarks, the average cost of an hour of downtime in manufacturing can exceed $250,000—a staggering figure that underlines the urgency for more effective maintenance strategies. The financial and strategic consequences are even more severe in industries with just-in-time production or critical service delivery requirements.
Predictive maintenance emerges as a powerful solution to this growing problem. It transforms traditional maintenance models by shifting the approach from reactive or scheduled interventions to intelligent, data-driven predictions. By leveraging real-time machine data and predictive analytics, enterprises can avoid costly surprises, extend asset life, and increase operational agility. This shift is not just about technology; it is a strategic move toward resilience and competitiveness in the digital era.
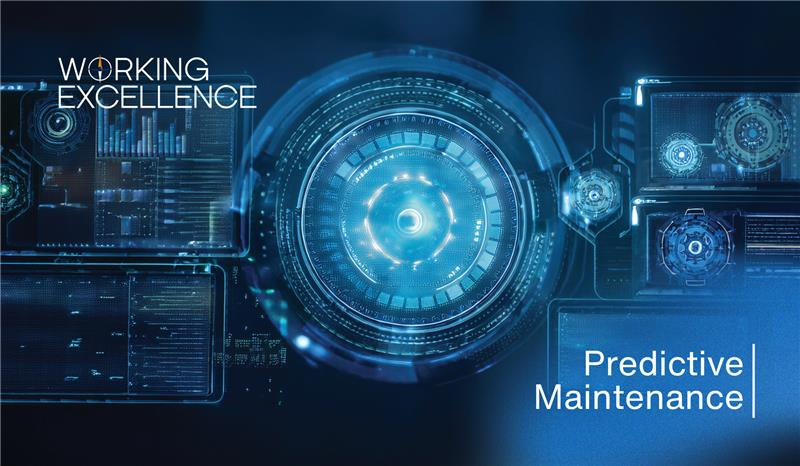
What Is Predictive Maintenance?
Predictive maintenance (PdM) is a forward-thinking maintenance strategy that uses data collected from connected sensors, equipment logs, and other real-time sources to predict asset failures before they occur. Unlike reactive maintenance, which responds to breakdowns after the fact, or preventive maintenance, which relies on time-based scheduling, predictive maintenance seeks to intervene at the optimal time—not too early and not too late.
This approach combines industrial Internet of Things (IoT) technologies, advanced analytics, artificial intelligence, and machine learning models to analyze patterns and identify anomalies in asset behavior. For example, if a motor begins to vibrate abnormally or a temperature sensor detects gradual overheating, predictive systems can flag the issue and trigger a maintenance intervention. This avoids unplanned failure, protects the integrity of assets, and reduces the waste associated with unnecessary servicing.
Predictive maintenance is widely considered a pillar of Industry 4.0 and smart manufacturing. It plays a pivotal role in enabling digital transformation by integrating maintenance into broader operational intelligence frameworks, where insights are generated in real time and shared across departments, facilities, and even continents.
Why Enterprises Are Shifting Toward Predictive Strategies
The traditional maintenance paradigms—whether reactive or based on predefined intervals—often fall short in the face of growing operational complexity and demand for uptime. Predictive maintenance offers a more intelligent and resource-efficient alternative, helping enterprises optimize maintenance activities while minimizing disruptions.
With extensive experience in IoT-driven analytics and asset performance management, Working Excellence helps enterprises implement predictive maintenance strategies that reduce downtime, lower costs, and extend asset lifecycles. This isn’t a concept we pitch—it's a practice we deliver at scale. Our track record with Fortune 500 clients in logistics, manufacturing, and infrastructure proves the power of predictive strategies.
Industry leaders are adopting predictive maintenance for several critical reasons:
Reduced Downtime: Predicting failures days or even weeks in advance allows organizations to perform repairs during scheduled windows, reducing disruption and extending equipment usability.
Lower Maintenance Costs: Predictive maintenance eliminates unnecessary preventive maintenance tasks and reduces emergency repair expenses, delivering significant cost savings over time.
Extended Asset Lifespan: By identifying the root causes of wear and failure, organizations can intervene precisely when needed, avoiding excessive strain on assets and maximizing their operational life.
Improved Safety and Compliance: Predictive systems help identify potentially dangerous failures before they escalate, promoting workplace safety and regulatory compliance.
Data-Driven Maintenance Culture: Enterprises that implement PdM gain access to continuous streams of asset intelligence, fostering a maintenance culture driven by insight, not instinct.
Our consultants integrate real-time sensor data, machine learning models, and predictive algorithms to forecast equipment failures before they happen. That level of foresight doesn’t just improve outcomes—it transforms maintenance from a cost center into a strategic differentiator.
The Technologies Powering Predictive Maintenance
Modern predictive maintenance is only possible because of the convergence of several advanced technologies. Together, they form a robust ecosystem that delivers actionable insights and supports enterprise-scale operations:
IoT Sensors: These devices collect real-time operational data such as temperature, vibration, pressure, flow, and humidity from industrial assets. Deployed strategically, IoT sensors serve as the frontline intelligence that fuels predictive analytics.
Edge Computing and Connectivity: To reduce latency and process data closer to the source, many enterprises deploy edge computing infrastructure. This ensures that critical insights are available without delay and can support time-sensitive decisions.
AI and Machine Learning Algorithms: Predictive maintenance systems utilize supervised and unsupervised learning models to detect deviations from normal behavior. Over time, these models become increasingly accurate, identifying complex patterns humans might overlook.
Cloud-Based Platforms and Digital Twins: Cloud platforms provide scalability and centralized visibility across locations. Digital twins—virtual replicas of physical assets—simulate scenarios, helping organizations assess the impact of interventions before they are made.
Enterprise Integration: PdM systems integrate with CMMS (Computerized Maintenance Management Systems), ERP software, and asset management platforms to ensure that insights lead to timely action across the enterprise.
Working Excellence’s predictive maintenance frameworks support scalable deployment across facilities and fleets, driving consistent performance and long-term savings. Whether you're managing thousands of HVAC units across retail locations or turbines in a power generation facility, we ensure your predictive infrastructure is enterprise-ready.
Predictive Maintenance in Action: Key Use Cases
From manufacturing plants to smart cities, predictive maintenance has found a home in virtually every sector that depends on complex equipment. The flexibility and scalability of PdM allow it to be customized to meet diverse operational needs:
Manufacturing: PdM prevents unexpected stoppages by continuously monitoring motor performance, conveyor alignment, and lubrication levels. This is crucial for maintaining output in high-speed environments.
Transportation and Logistics: Fleet managers use predictive analytics to anticipate engine, brake, and transmission issues. This reduces the risk of roadside failures and improves fleet availability.
Utilities and Energy: In power plants and grid infrastructure, predictive maintenance prevents critical failures in generators, transformers, and substations. It also improves asset utilization and regulatory compliance.
Facility Management: Property operators can predict failures in elevators, HVAC systems, and lighting infrastructure, ensuring seamless service for tenants and minimizing emergency maintenance calls.
Oil and Gas: PdM is used to monitor pipeline pressure, valve operations, and drilling rig performance, reducing the risks associated with catastrophic failures.
By enabling proactive maintenance scheduling, we help organizations avoid costly interruptions and optimize maintenance resources. These outcomes are not just potential benefits—they are proven results delivered through our ongoing partnerships.
How to Implement Predictive Maintenance in Your Organization
A successful predictive maintenance program is more than installing sensors and buying software. It requires a well-planned, phased approach grounded in operational insight and supported by organizational commitment. Working Excellence guides enterprises through each step of implementation:
Assessment and Goal Definition: We start by evaluating your current maintenance maturity, identifying critical assets, and defining the KPIs that matter to your business.
Data Infrastructure Readiness: Our team works with you to ensure you have the right sensors, data storage, and connectivity solutions in place.
Model Development and Training: Using historical data, we help train predictive models tailored to your asset behavior. We validate their accuracy and fine-tune them for your environment.
Integration with Workflows: Predictive alerts are connected to your existing maintenance and operations processes. This ensures that insights result in timely, effective actions.
Continuous Improvement: Once deployed, we support performance monitoring and model refinement. As more data becomes available, your PdM system becomes smarter and more accurate.
This isn't about adopting a tool—it's about operational transformation. With our support, enterprises can go beyond the pilot phase and build predictive maintenance programs that scale across regions, business units, and even continents.
Your Next Step: Turn Uncertainty Into Operational Excellence
Predictive maintenance is rapidly becoming the gold standard for enterprises seeking to unlock operational agility, cost control, and long-term asset value. It empowers decision-makers with visibility, foresight, and precision—qualities essential in today’s complex, always-on business environment.
Partner with us to stay ahead of equipment issues and unlock a new era of intelligent asset management—where reliability and efficiency lead the way. With extensive experience in IoT-driven analytics and asset performance management, we help enterprises implement predictive maintenance strategies that reduce downtime, lower costs, and extend asset lifecycles.
The time for predictive maintenance is now. Will your organization continue reacting to problems—or start predicting them?
Let’s build your predictive advantage. Connect with Working Excellence today.
Frequently Asked Questions
What is predictive maintenance and how does it work in large enterprises?
Predictive maintenance is a data-driven maintenance strategy that leverages IoT sensors, machine learning, and advanced analytics to forecast equipment failures before they occur. In large enterprises, predictive maintenance systems are integrated with asset performance management platforms, allowing for real-time monitoring, anomaly detection, and proactive maintenance scheduling across complex operations. By predicting when an asset will likely fail, organizations can minimize downtime, optimize maintenance costs, and extend the useful life of critical equipment.
What technologies are essential for implementing predictive maintenance at scale?
How does predictive maintenance reduce costs and improve ROI for enterprises?
What are some real-world use cases of predictive maintenance in industry?
How can an enterprise start implementing predictive maintenance successfully?